THIN LAYER DRYING KINETICS OF AMARANTH (Amaranthus cruentus) GRAINS IN A NATURAL CONVECTION SOLAR TENT DRYER
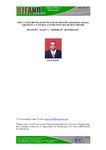
View/ Open
Date
2010-03Author
Ronoh, EK
Kanali, CL
Mailutha, JT
Shitanda, D
Metadata
Show full item recordAbstract
An experimental solar tent dryer under natural convection was used to study thin layer drying kinetics of amaranth (Amaranthus cruentus) grains. Drying of grains in the dryer was carried out on a drying rack having two layers; top and bottom. The ambient temperature and relative humidity ranged from 22.6–30.4oC and 25–52%, respectively, while the inside temperature and relative humidity in the solar dryer ranged from 31.2–54.7oC and 22–34%, respectively. Freshly harvested amaranth grains with an average moisture content of 64% were dried under the solar tent dryer for seven hours to a final moisture content of 7% (dry basis). A non-linear regression analysis was used to evaluate six thin layer drying models (viz., Newton, Page, Modified Page, Henderson & Pabis, Logarithmic and Wang & Singh) for amaranth grains. The models were compared using coefficient of determination (R2), root mean square error (RMSE), reduced chi-square (χ2) and prediction performance (ηp) in order to determine the one that best described thin layer drying of amaranth grains. The results show that the Page model satisfactorily described the drying of amaranth grains with R2 of 0.9980, χ2 of 0.00016 and RMSE of 0.01175 for bottom layer and R2 of 0.9996, χ2 of 0.00003 and RMSE of 0.00550 for top layer of the drying rack. Based on a ±5% residual error interval, the Page model attained the highest prediction performance (ηp = 80%) when drying the grains in both layers of the dryer. This shows that there was a good agreement between the predicted and experimental moisture changes during solar drying of amaranth grains under natural convection. The transport of water during dehydration was described by applying the Fick’s diffusion model and the effective moisture diffusivity for solar tent drying of amaranth grains was found to be 5.88×10-12 m2s-1 at the bottom layer and 6.20×10-12 m2s-1 at the top layer. High temperatures developed at the top layer of the dryer led to high effective moisture diffusivity and this showed that temperature strongly influences the mechanism of moisture removal from the grains.